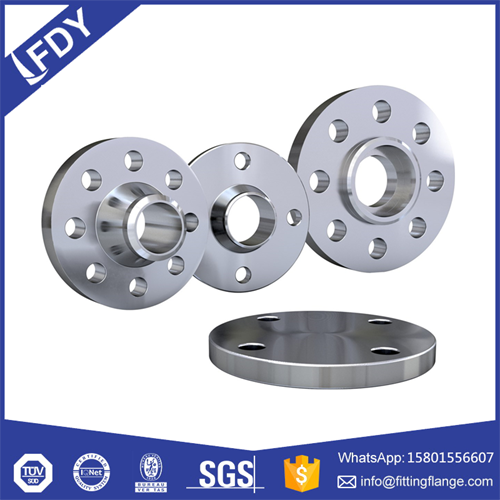
When it comes to installing alloy steel flanges, several key tips can ensure a proper and durable installation.
First, precise measurement is crucial. Accurately measure the pipe diameter and flange dimensions to ensure a perfect fit. Any discrepancies can lead to leaks or improper alignment.
Before installation, thoroughly clean the flange surfaces and the mating pipe ends. Remove any dirt, debris, or rust that could affect the sealing performance. Inspect the flange gasket as well; it should be in good condition and of the correct material and thickness for the application.
During installation, use proper alignment tools. Ensure the flanges are perfectly centered and parallel to each other. Tighten the bolts in a specific pattern, usually starting from the center and working outward in a crisscross manner. This helps distribute the clamping force evenly.
Apply the correct torque to the bolts. Over-tightening can damage the flange or the bolts, while under-tightening may result in leaks. Use a calibrated torque wrench and follow the manufacturer’s recommended torque values.
After installation, conduct a pressure test to check for any leaks. This is essential to identify and rectify any potential issues before the system is put into operation.
By following these tips, the installation of alloy steel flanges can be carried out effectively, minimizing the risk of leaks and ensuring the integrity and reliability of the piping system.