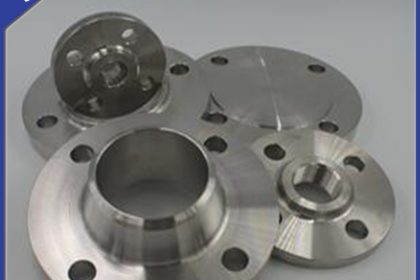
Forged flanges are an essential component in many industrial processes, especially in piping systems. These versatile and durable fittings can streamline industrial processes in several ways.
- Strength and Durability: Forged flanges are manufactured by subjecting metal to extreme pressure and heat, resulting in a product that is incredibly strong and resistant to wear and tear. The forging process aligns the grain structure of the metal, making it more robust and able to withstand high-pressure and high-temperature environments. This strength and durability are crucial for ensuring the integrity of piping systems and preventing leaks or failures that could disrupt industrial processes.
- Leak Prevention: One of the primary purposes of using forged flanges is to connect different sections of a piping system securely. The flange acts as a seal between pipes, preventing leakage of fluids or gases. The precise machining and tight sealing ability of forged flanges significantly reduce the risk of leaks, which can be costly and dangerous in industrial settings. By eliminating leaks or potential failures, forged flanges streamline industrial processes by minimizing downtime and improving overall safety.
- Easy Installation and Maintenance: Forged flanges are designed to be easily installed and removed, making them highly convenient for maintenance and repair work. Their standardized dimensions and connection methods allow for interchangeability, enabling quick and efficient replacement of parts. This ease of installation and maintenance saves time and reduces labor costs associated with downtime during repairs or system modifications.
- Versatility: Forged flanges come in various shapes, sizes, and materials, allowing them to be used in a wide range of industrial processes. They can be customized to suit specific requirements such as pressure ratings, temperature limits, or corrosive environments. This versatility makes forged flanges suitable for diverse applications in industries such as oil and gas, petrochemicals, power generation, and water treatment. By providing a flexible and adaptable solution, forged flanges streamline industrial processes by simplifying procurement and reducing the need for multiple types of fittings.
- Improved Flow Characteristics: The design of forged flanges, especially their smooth inner surface, promotes optimum flow characteristics in piping systems. Their precise dimensions and machined surfaces minimize turbulence, pressure drops, and restrictions, resulting in efficient fluid or gas flow. By improving the flow characteristics, forged flanges enhance the overall performance of industrial processes, reduce energy consumption, and maximize productivity.
- Enhanced Safety: Industrial processes often involve the transportation of hazardous or flammable substances. Using forged flanges ensures a robust connection between pipes, minimizing the risk of leaks or failures. This enhanced safety not only protects workers and the environment but also reduces the potential for accidents or unplanned shutdowns. By providing a secure and reliable connection, forged flanges streamline industrial processes by maintaining a safe working environment and regulatory compliance.
Forged flanges play a critical role in streamlining industrial processes. Their strength, durability, leak prevention capabilities, easy installation and maintenance, versatility, improved flow characteristics, and enhanced safety combine to create a more efficient and reliable piping system. By choosing forged flanges, industrial facilities can optimize their operations, minimize downtime, reduce costs, and ensure long-term performance and safety.